Fibre Optics
Development of Fibre-Based Gas Sensor for Inaccessible Locations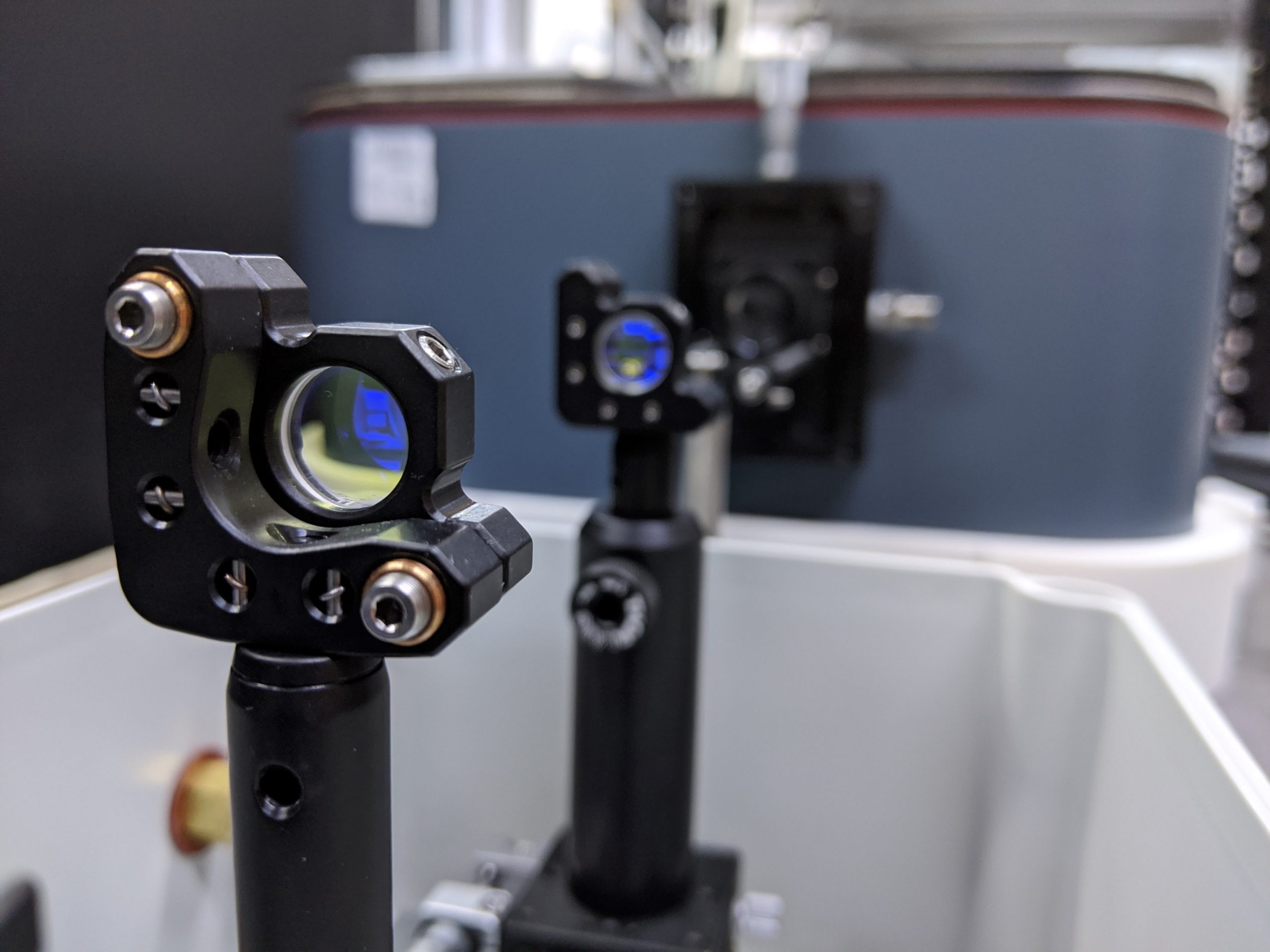
Point of contact: Dr Bill MacPherson
Optical gas sensor technologies can provide important data that can be used to infer the presence of chemical ageing processes that can occur within a hermetically sealed system. This project aims to achieve sensitive and selective gas speciation measurements while also considering the chemical and physical constraints with regards to the system within which the sensor is located.
The detection of certain gas species can provide important information of the various chemical ageing processes occurring within a system. Regarding this project’s current application, it is critical that this detection mechanism is non-extracting and non-destructive within a hermetically sealed system and is capable of achieving high sensitivity and selective measurements. The primary gases of interest are O2, NOx and COx.
Currently, the investigation of broad-band cavity-enhanced absorption spectroscopy is being conducted. The utilisation of a laser-driven light source, capable of fibre coupling, allows for broad-band light to be coupled into an optical cavity formed by two highly reflective mirrors. The light leaked from the cavity is then dispersed through a spectrometer and is detected by a photomultiplier tube. The concentration level of gases can then be determined by the optical absorption that occurs within the gas cell.
Research Team: Tamer Y. Cosgun, Bill MacPherson, Simon Brooks (AWE)
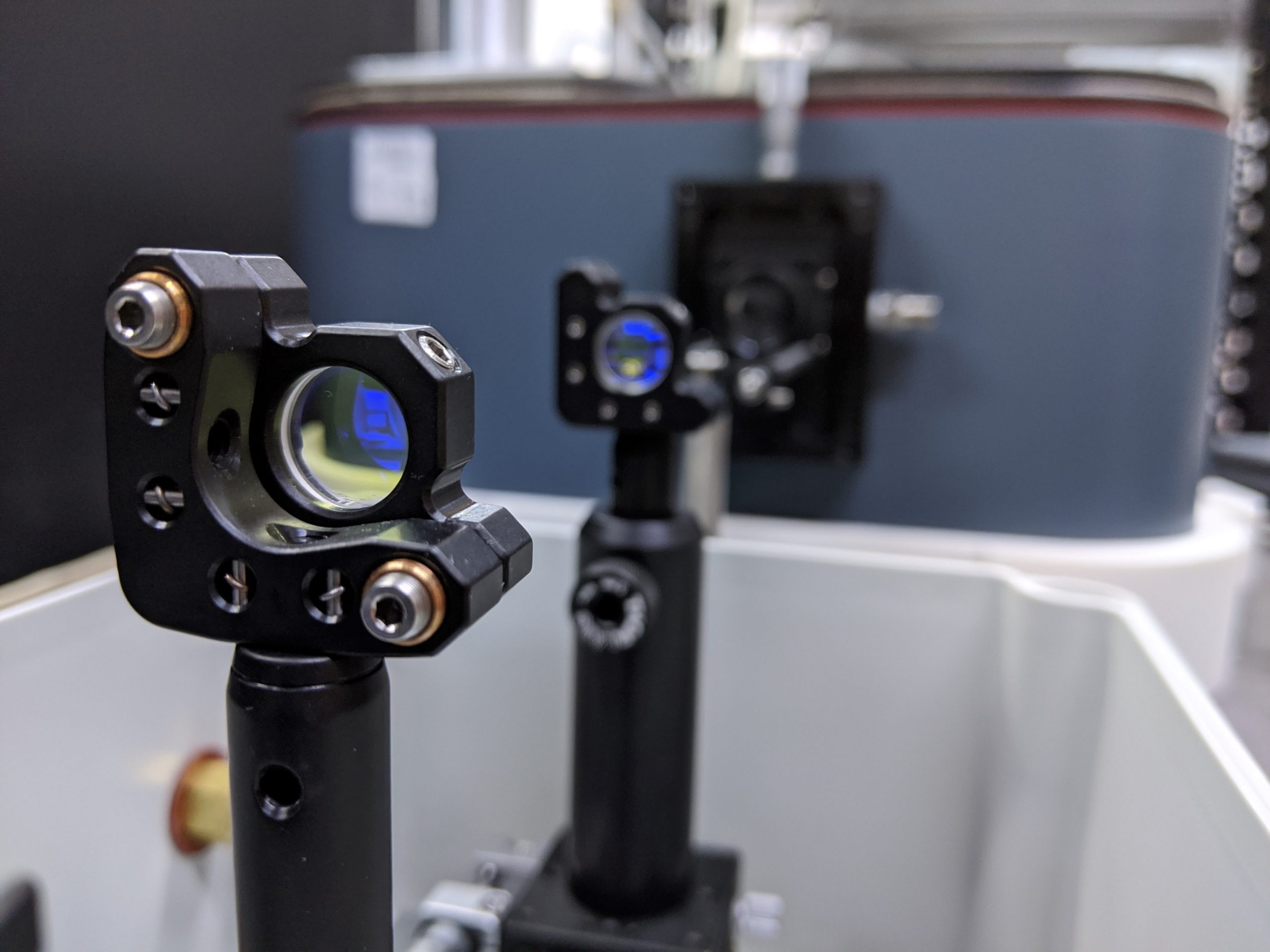
Point of contact: Dr Bill MacPherson
Optical gas sensor technologies can provide important data that can be used to infer the presence of chemical ageing processes that can occur within a hermetically sealed system. This project aims to achieve sensitive and selective gas speciation measurements while also considering the chemical and physical constraints with regards to the system within which the sensor is located.
The detection of certain gas species can provide important information of the various chemical ageing processes occurring within a system. Regarding this project’s current application, it is critical that this detection mechanism is non-extracting and non-destructive within a hermetically sealed system and is capable of achieving high sensitivity and selective measurements. The primary gases of interest are O2, NOx and COx.
Currently, the investigation of broad-band cavity-enhanced absorption spectroscopy is being conducted. The utilisation of a laser-driven light source, capable of fibre coupling, allows for broad-band light to be coupled into an optical cavity formed by two highly reflective mirrors. The light leaked from the cavity is then dispersed through a spectrometer and is detected by a photomultiplier tube. The concentration level of gases can then be determined by the optical absorption that occurs within the gas cell.
Research Team: Tamer Y. Cosgun, Bill MacPherson, Simon Brooks (AWE)
Hollow-core anti-resonant negative curvature optical fibres (HC-ARF) for high-peak power laser applications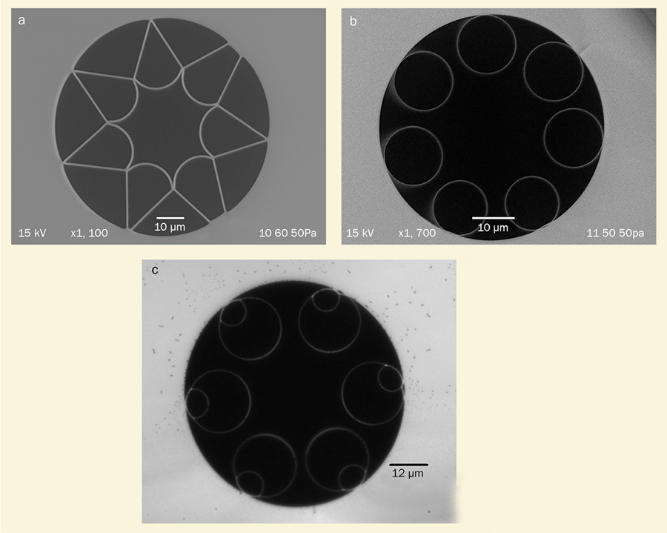
Point of contact: Prof. Duncan Hand
Hollow-core anti-resonant negative curvature optical fibres exhibit extraordinary transmission capability and flexibility for delivering high peak power ultrashort laser pulses. This project aims to find and break the limits of these fibres, and to explore their great potential in high peak power applications.
When light propagates through the quasi-vacuum environment in hollow core optical fibres instead of silica in conventional fibres, transmission is no longer limited by solid materials. The anti-resonant glass layer with a “negative curvature” structure surrounding the core can confine 99% of the mode energy in the air core, providing an ultralow attenuation. The combination of these features enables ultrashort pulses to propagate through the fibre with ultralow loss and ultrahigh damage threshold. The goal of this project is to investigate and expand the capability of hollow core anti-resonant guiding fibres (HC-ARF) (provided by the University of Bath) to transmit ultrashort laser pulses in all wavelength ranges, including the characterization and improvement of their important transmission properties such as transmission loss, bending loss, dispersion, nonlinearity, polarization maintaining, mode quality, coupling efficiency, and maximum transmittable power. High-power laser applications such as laser precision manufacturing and laser medical treatment can benefit from the result of this project. In cooperation with our industrial partners, the practical applications of ultrafast laser delivered by HC-ARF is becoming more reliable, flexible and convenient by all means.
This project was supported by projects EP/M025888/1, EP/I01246X/1, EP/M025381/1, and EP/I011315 financed by Engineering and Physical Sciences Research Council, UK.
Research Team: Shouyue Wu, Bartlomiej Siwicki, Richard M. Carter, Jonathan D. Shephard, Duncan P. Hand, EPSRC, Coherent, M-Solv, Litron Lasers, University of Bath, Powerlase
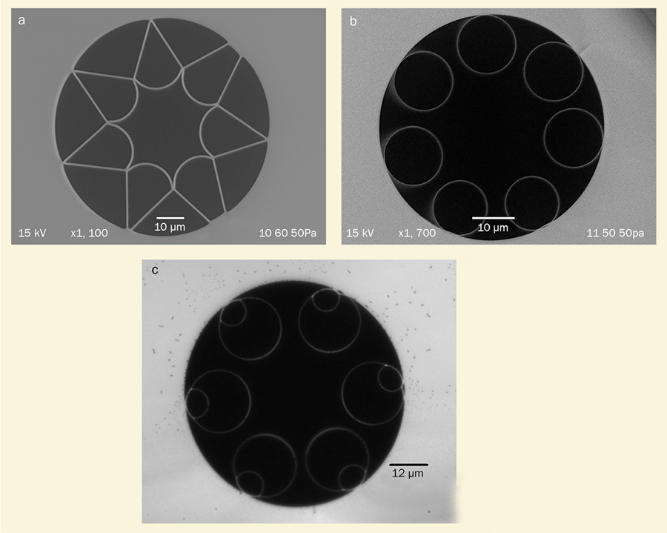
Point of contact: Prof. Duncan Hand
Hollow-core anti-resonant negative curvature optical fibres exhibit extraordinary transmission capability and flexibility for delivering high peak power ultrashort laser pulses. This project aims to find and break the limits of these fibres, and to explore their great potential in high peak power applications.
When light propagates through the quasi-vacuum environment in hollow core optical fibres instead of silica in conventional fibres, transmission is no longer limited by solid materials. The anti-resonant glass layer with a “negative curvature” structure surrounding the core can confine 99% of the mode energy in the air core, providing an ultralow attenuation. The combination of these features enables ultrashort pulses to propagate through the fibre with ultralow loss and ultrahigh damage threshold. The goal of this project is to investigate and expand the capability of hollow core anti-resonant guiding fibres (HC-ARF) (provided by the University of Bath) to transmit ultrashort laser pulses in all wavelength ranges, including the characterization and improvement of their important transmission properties such as transmission loss, bending loss, dispersion, nonlinearity, polarization maintaining, mode quality, coupling efficiency, and maximum transmittable power. High-power laser applications such as laser precision manufacturing and laser medical treatment can benefit from the result of this project. In cooperation with our industrial partners, the practical applications of ultrafast laser delivered by HC-ARF is becoming more reliable, flexible and convenient by all means.
This project was supported by projects EP/M025888/1, EP/I01246X/1, EP/M025381/1, and EP/I011315 financed by Engineering and Physical Sciences Research Council, UK.
Research Team: Shouyue Wu, Bartlomiej Siwicki, Richard M. Carter, Jonathan D. Shephard, Duncan P. Hand, EPSRC, Coherent, M-Solv, Litron Lasers, University of Bath, Powerlase
Sensors in Additive Layer Manufactured Components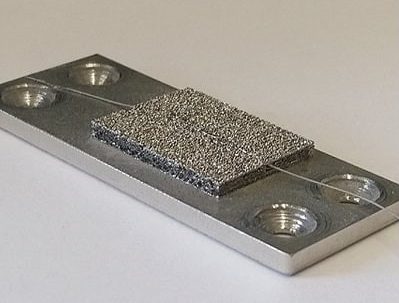
Point of contact: Dr Bill MacPherson
Components manufactured by Additive Layer Manufacture (ALM), commonly referred to as 3D printing, are increasingly being used in applications where traditional manufacturing routes are not feasible. These components benefit from in-situ monitoring and this project aims to develop techniques for embedding novel sensor components.
Distributed temperature and strain sensing within metallic ALM structures is important to monitor component health and help to predict potential failure mechanisms. The goal of this project is to investigate novel strategies that enable integration of optical fibre based sensors into metallic ALM components. The project aims to demonstrate the ability to produce distributed arrays of metal embedded sensors with a primary goal leading towards the production of an embedded array of temperature sensors.
Embedding strategies including fibre metallisation, ALM process optimisation, and post embedding characterisation and treatment will be considered. Initial stages of this work will concentrate on using conventional communications grade single mode fibre, incorporating Fibre Bragg Gratings, as the core sensing technology.
Research Team: Ben Michie, Bill MacPherson, Robert Maier
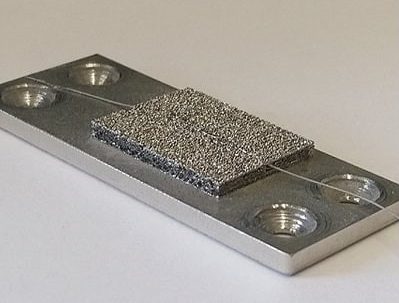
Point of contact: Dr Bill MacPherson
Components manufactured by Additive Layer Manufacture (ALM), commonly referred to as 3D printing, are increasingly being used in applications where traditional manufacturing routes are not feasible. These components benefit from in-situ monitoring and this project aims to develop techniques for embedding novel sensor components.
Distributed temperature and strain sensing within metallic ALM structures is important to monitor component health and help to predict potential failure mechanisms. The goal of this project is to investigate novel strategies that enable integration of optical fibre based sensors into metallic ALM components. The project aims to demonstrate the ability to produce distributed arrays of metal embedded sensors with a primary goal leading towards the production of an embedded array of temperature sensors.
Embedding strategies including fibre metallisation, ALM process optimisation, and post embedding characterisation and treatment will be considered. Initial stages of this work will concentrate on using conventional communications grade single mode fibre, incorporating Fibre Bragg Gratings, as the core sensing technology.
Research Team: Ben Michie, Bill MacPherson, Robert Maier
Surgical
Endoscopically deployable optics for picosecond laser surgery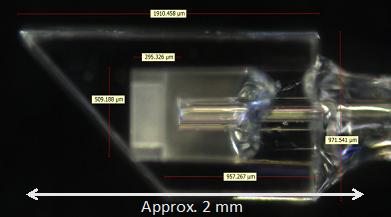
Point of contact: Prof. Jonathan Shephard
The ultimate aim of the work is to prove concepts for practically deployable optical elements for the endoscopic delivery of ps laser light via novel hollow core fibres. We address existing technological barriers that need to be overcome in order to move towards practical deployment in a clinical environment.
The ultimate aim of the work is to prove concepts for practically deployable optical elements for the endoscopic delivery of ps laser light via novel hollow core fibres. This follows directly on from our EPSRC project aimed at developing new laser surgical techniques for early stage colorectal tumour surgery. The overall concept that ps laser light can be used to precisely resect tumours tissue with virtually no collateral damage to surrounding healthy tissue was well proven. This project will build on these excellent results and aim to address existing technological barriers in miniaturisation and integration that need to be overcome in order to move towards practical deployment in a clinical environment.
This work is funded through Multi-modal Manufacturing of Medical Devices (4MD) by EPSRC (EP/P027415/1).
Research Team: Jon Shephard, Robert Thomson, Rainer Beck, Donald Risbridger (IPaQS), David Jayne, Nick West (University of Leeds)
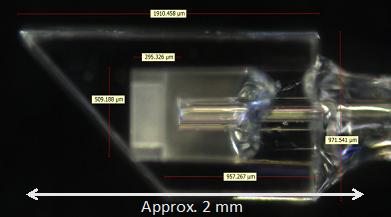
Point of contact: Prof. Jonathan Shephard
The ultimate aim of the work is to prove concepts for practically deployable optical elements for the endoscopic delivery of ps laser light via novel hollow core fibres. We address existing technological barriers that need to be overcome in order to move towards practical deployment in a clinical environment.
The ultimate aim of the work is to prove concepts for practically deployable optical elements for the endoscopic delivery of ps laser light via novel hollow core fibres. This follows directly on from our EPSRC project aimed at developing new laser surgical techniques for early stage colorectal tumour surgery. The overall concept that ps laser light can be used to precisely resect tumours tissue with virtually no collateral damage to surrounding healthy tissue was well proven. This project will build on these excellent results and aim to address existing technological barriers in miniaturisation and integration that need to be overcome in order to move towards practical deployment in a clinical environment.
This work is funded through Multi-modal Manufacturing of Medical Devices (4MD) by EPSRC (EP/P027415/1).
Research Team: Jon Shephard, Robert Thomson, Rainer Beck, Donald Risbridger (IPaQS), David Jayne, Nick West (University of Leeds)
A fluorescence guided steerable laser tool for precision resection of early stage cancers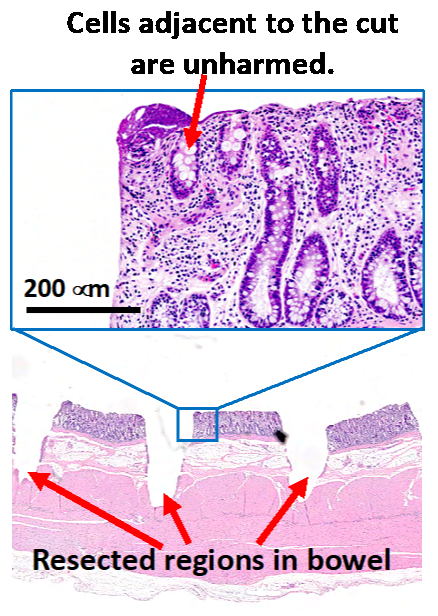
Point of contact: Prof. Duncan Hand
We develop procedures based on ultrashort laser pulses for the successful colonic epithelial laser ablation. This is a potential alternative to overcome limitations of conventional diathermic techniques in terms of precision and thermal damage.
In the UK 40,000 people are diagnosed every year with colorectal cancer. Existing procedures for surgical treatment use relatively cumbersome electrical cutting devices to apply heat to the tissue are challenging to perform due to restricted access and a lack of fine control for the surgeon.
Infrared lasers are attractive for surgery because the water in human tissue strongly absorbs this radiation. Additionally, “ultrafast” i.e. picosecond pulsed lasers deliver energy in such short pulses that thermal effects are minimal and tissue can be ablated with the resulting crater restricted only to the area on which the pulse was incident. Therefore, by precisely and flexibly delivering the energy to specific tumorous areas they can be cleanly removed minimising both damage to surrounding tissue and the risk of bowel perforation.
Through our collaboration we will realise the full potential of novel hollow-core fibres and create a novel steerable surgical tool guided by the fluorescent marker. Our partnership consists of experts in high power laser applications and biophotonics at Heriot-Watt University and clinical expertise at the University of Leeds. Together we will exploit this technology to develop a life-saving colorectal surgical procedure transferable to other life-threatening conditions.
This work was funded through Healthcare Impact Partnership by EPSRC (grant number EP/N02494X/1).
Research Team: Jon Shephard, Duncan Hand, Robert Thomson, Rainer Beck (HWU), David Jayne, Nick West (University of Leeds)
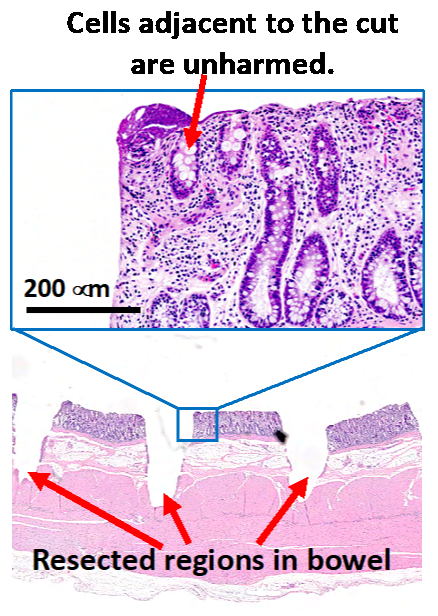
Point of contact: Prof. Duncan Hand
We develop procedures based on ultrashort laser pulses for the successful colonic epithelial laser ablation. This is a potential alternative to overcome limitations of conventional diathermic techniques in terms of precision and thermal damage.
In the UK 40,000 people are diagnosed every year with colorectal cancer. Existing procedures for surgical treatment use relatively cumbersome electrical cutting devices to apply heat to the tissue are challenging to perform due to restricted access and a lack of fine control for the surgeon.
Infrared lasers are attractive for surgery because the water in human tissue strongly absorbs this radiation. Additionally, “ultrafast” i.e. picosecond pulsed lasers deliver energy in such short pulses that thermal effects are minimal and tissue can be ablated with the resulting crater restricted only to the area on which the pulse was incident. Therefore, by precisely and flexibly delivering the energy to specific tumorous areas they can be cleanly removed minimising both damage to surrounding tissue and the risk of bowel perforation.
Through our collaboration we will realise the full potential of novel hollow-core fibres and create a novel steerable surgical tool guided by the fluorescent marker. Our partnership consists of experts in high power laser applications and biophotonics at Heriot-Watt University and clinical expertise at the University of Leeds. Together we will exploit this technology to develop a life-saving colorectal surgical procedure transferable to other life-threatening conditions.
This work was funded through Healthcare Impact Partnership by EPSRC (grant number EP/N02494X/1).
Research Team: Jon Shephard, Duncan Hand, Robert Thomson, Rainer Beck (HWU), David Jayne, Nick West (University of Leeds)
Laser 3D printing of micro-scale graded shape memory components for in-vivo actuated medical devices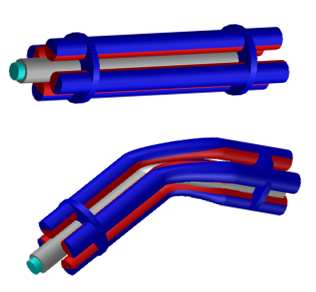
Point of contact: Prof. Duncan Hand
The project involves fabrication of sub-mm scale Shape Memory Alloy components using a high-precision LIFT (laser-induced forward transfer) process. The fabricated actuators will be then used as a part of medical devices for precise in-vivo motion.
Shape memory alloys (SMAs) are currently manufactured either in very thin films by vapour deposition or in bulk by casting or powder metallurgy techniques. None of these processes provides the spatially controlled functionalisation required for novel medical applications. Our approach is based on an enhancement of the high precision laser LIFT (Laser Induced Forward Transfer) process – that can build components from sub-micron layers of different materials – in combination with highly localised thermal tailoring of SMA material parameters. We will use laser pulses to sequentially “print” thin “sub-voxels” of metal films onto a substrate, in order to construct voxels each consisting of a number of sub-voxel layers of different metals. Key to our concept is the use of a multi-track substrate reel-to-reel donor tape, with each ‘track’ consisting of a coating of a thin film of a different component material for an SMA alloy. By altering the laser parameters, subsequent thermal treatment will be used to provide control of interdiffusion within and between voxels providing very tight localised control of composition. 3D microstructures will hence be constructed by continuing to add additional voxels. Example applications include precise incision, tissue identification, tactile sensing for disease and tweezing, as well as more ambitious shape transformations for “unpacking” structures in situ and “intelligent” stents and patches.
Research Team: Bartłomiej Siwicki, Logaheswari Muniraj, Robert L. Reuben, and Duncan P. Hand (HWU), Riccardo Geremia (Oxford Lasers Ltd.), Nick Weston (Renishaw)
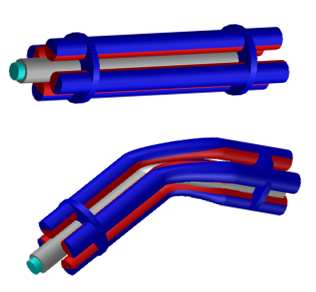
Point of contact: Prof. Duncan Hand
The project involves fabrication of sub-mm scale Shape Memory Alloy components using a high-precision LIFT (laser-induced forward transfer) process. The fabricated actuators will be then used as a part of medical devices for precise in-vivo motion.
Shape memory alloys (SMAs) are currently manufactured either in very thin films by vapour deposition or in bulk by casting or powder metallurgy techniques. None of these processes provides the spatially controlled functionalisation required for novel medical applications. Our approach is based on an enhancement of the high precision laser LIFT (Laser Induced Forward Transfer) process – that can build components from sub-micron layers of different materials – in combination with highly localised thermal tailoring of SMA material parameters. We will use laser pulses to sequentially “print” thin “sub-voxels” of metal films onto a substrate, in order to construct voxels each consisting of a number of sub-voxel layers of different metals. Key to our concept is the use of a multi-track substrate reel-to-reel donor tape, with each ‘track’ consisting of a coating of a thin film of a different component material for an SMA alloy. By altering the laser parameters, subsequent thermal treatment will be used to provide control of interdiffusion within and between voxels providing very tight localised control of composition. 3D microstructures will hence be constructed by continuing to add additional voxels. Example applications include precise incision, tissue identification, tactile sensing for disease and tweezing, as well as more ambitious shape transformations for “unpacking” structures in situ and “intelligent” stents and patches.
Research Team: Bartłomiej Siwicki, Logaheswari Muniraj, Robert L. Reuben, and Duncan P. Hand (HWU), Riccardo Geremia (Oxford Lasers Ltd.), Nick Weston (Renishaw)
Novel Technologies to Enhance Minimally Invasive Surgery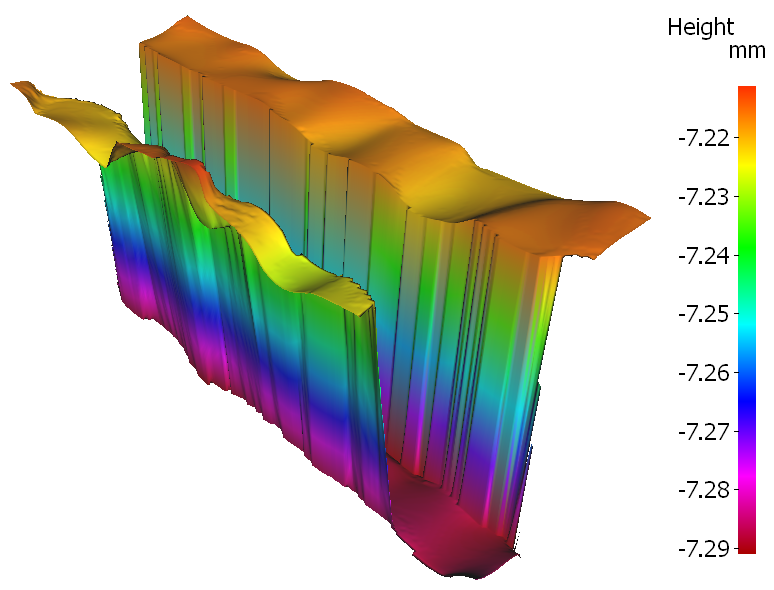
Point of contact: Prof. Jonathan Shephard
Infrared ultrashort pulsed lasers show great promise towards surgical applications, offering high precision and compatibility with minimally invasive techniques. The objective of this project is to further improve the precision and efficiency of ultrashort pulsed laser ablation of soft biological tissues, which would in turn develop current endoscopic procedures.
This project aims to further develop the application of infrared ultrashort pulsed picosecond lasers within surgical environments. Laser surgery using ultrafast picosecond/femtosecond lasers can greatly enhance both the precision and effectiveness of treatment for a wide range of diseases. Highly flexible anti-resonant microstructured fibres will be used to deliver these high energy pulses as they offer both high damage thresholds and flexible, low-loss transmission, enabling high-powered endoscopic delivery within the complex structures of the body. Novel beam steering and manipulation solutions will be investigated and combined with optical monitoring technologies, ideally for implementation in a clinical environment.
Bessel beams have shown numerous advantages over more conventional focused Gaussian beams in industrial material processing applications, including less sensitivity to focal position and possessing self-healing/diffraction resistant behaviour (albeit over a limited range experimentally). These traits have the potential to be of significance in minimally invasive surgical procedures, where inhomogeneity and scattering are both important considerations.
Research Team: Donald Risbridger, Jonathan Shephard, Rainer Beck, Mr. Syam Mohan
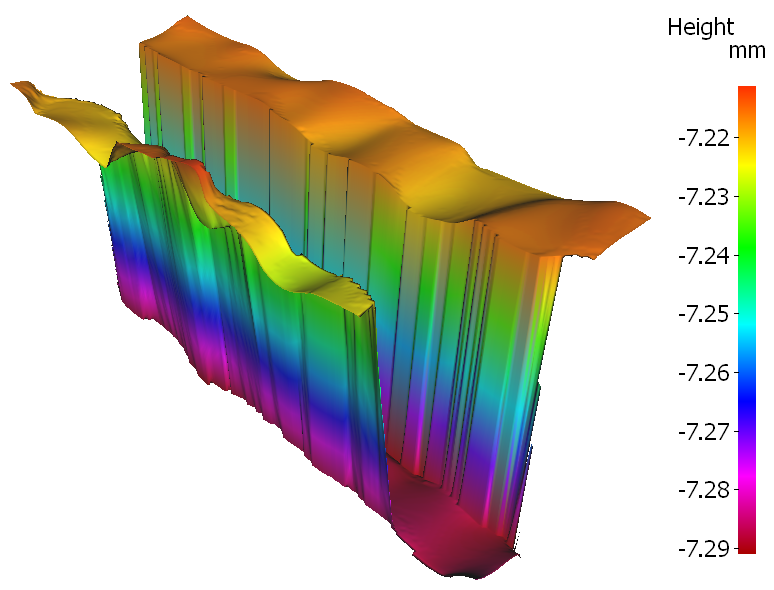
Point of contact: Prof. Jonathan Shephard
Infrared ultrashort pulsed lasers show great promise towards surgical applications, offering high precision and compatibility with minimally invasive techniques. The objective of this project is to further improve the precision and efficiency of ultrashort pulsed laser ablation of soft biological tissues, which would in turn develop current endoscopic procedures.
This project aims to further develop the application of infrared ultrashort pulsed picosecond lasers within surgical environments. Laser surgery using ultrafast picosecond/femtosecond lasers can greatly enhance both the precision and effectiveness of treatment for a wide range of diseases. Highly flexible anti-resonant microstructured fibres will be used to deliver these high energy pulses as they offer both high damage thresholds and flexible, low-loss transmission, enabling high-powered endoscopic delivery within the complex structures of the body. Novel beam steering and manipulation solutions will be investigated and combined with optical monitoring technologies, ideally for implementation in a clinical environment.
Bessel beams have shown numerous advantages over more conventional focused Gaussian beams in industrial material processing applications, including less sensitivity to focal position and possessing self-healing/diffraction resistant behaviour (albeit over a limited range experimentally). These traits have the potential to be of significance in minimally invasive surgical procedures, where inhomogeneity and scattering are both important considerations.
Research Team: Donald Risbridger, Jonathan Shephard, Rainer Beck, Mr. Syam Mohan
Manufacturing
High Quality, High-Speed Engraving Using High Average Power Nanosecond Pulse Fibre Lasers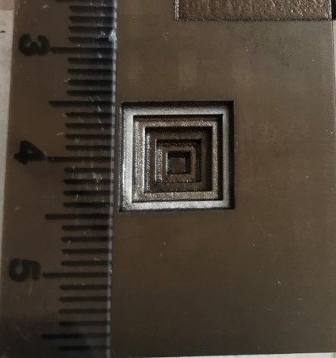
Point of contact: Prof. Duncan Hand
High average power nanosecond lasers offer high throughput at the expense of process quality. This project, funded by SPI Lasers and the University, investigates laser-material interaction and processing strategies in the high power regime in order to propose an ideal system for high throughput and quality laser applications such as engraving.
Engraving of metals using moderate average power (~20W) nanosecond (ns) pulsed fibre lasers is well established. Examples of very high-quality 3D engraving are available, for instance in the creation of dies for coin manufacture, where very low surface roughness is required together with high dimensional accuracy. Although process rates are reasonable (a few cubic mm/second) there is a demand for higher productivity and hence higher average power nanosecond pulsed fibre lasers have been developed for this and other applications (100 – 200W). However, simply using similar but scaled up process parameters for these higher power lasers do not yield similar surface quality, nor even the expected process rate. This project therefore seeks to understand and overcome these issues. The work is undertaken using the current pulsed laser product range of SPI Lasers together with laser products in development. We are examining the range of physical effects that occur when using high power nanosecond pulses with different temporal shapes and peak powers, as well investigating different scanning strategies and parametric combinations that will produce fast and high-quality results.
Research Team: Stephen D. Dondieu, Krystian L. Wlodarczyk, Robert L. Reuben, Duncan P. Hand, Paul Harrison (SPI Lasers), Adam Rosowski (SPI lasers), Jack Gabzdyl (SPI Lasers)
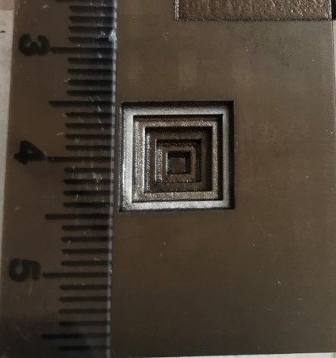
Point of contact: Prof. Duncan Hand
High average power nanosecond lasers offer high throughput at the expense of process quality. This project, funded by SPI Lasers and the University, investigates laser-material interaction and processing strategies in the high power regime in order to propose an ideal system for high throughput and quality laser applications such as engraving.
Engraving of metals using moderate average power (~20W) nanosecond (ns) pulsed fibre lasers is well established. Examples of very high-quality 3D engraving are available, for instance in the creation of dies for coin manufacture, where very low surface roughness is required together with high dimensional accuracy. Although process rates are reasonable (a few cubic mm/second) there is a demand for higher productivity and hence higher average power nanosecond pulsed fibre lasers have been developed for this and other applications (100 – 200W). However, simply using similar but scaled up process parameters for these higher power lasers do not yield similar surface quality, nor even the expected process rate. This project therefore seeks to understand and overcome these issues. The work is undertaken using the current pulsed laser product range of SPI Lasers together with laser products in development. We are examining the range of physical effects that occur when using high power nanosecond pulses with different temporal shapes and peak powers, as well investigating different scanning strategies and parametric combinations that will produce fast and high-quality results.
Research Team: Stephen D. Dondieu, Krystian L. Wlodarczyk, Robert L. Reuben, Duncan P. Hand, Paul Harrison (SPI Lasers), Adam Rosowski (SPI lasers), Jack Gabzdyl (SPI Lasers)
Laser Post-Processing of Additively Manufactured Metal Parts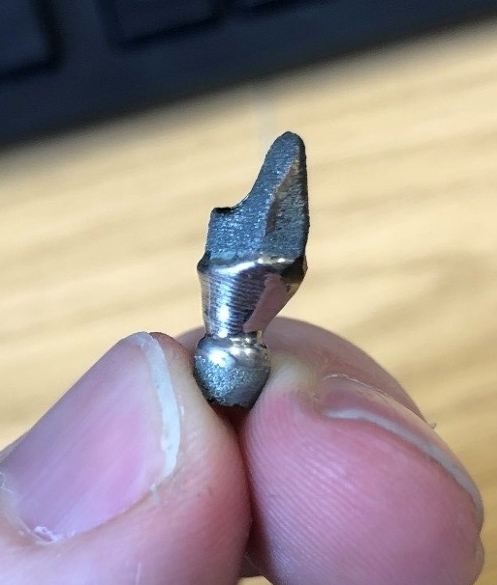
Point of contact: Prof. Duncan Hand
This project supported by Renishaw and EPSRC, is developing a laser polishing technique working to improve the surface finish of additively manufactured metal parts. This method offers advantages over currently used processing methods by allowing greater selectivity of the localised surface finish and simpler process automation for bespoke parts.
Additively manufactured components have a high surface roughness in their as-built state rendering them unsuitable for most applications without some degree of post-processing. Commonly used methods include mechanical polishing which for bespoke parts is a time-consuming semi-manual process requiring a skilled worker. Another common method is electro-chemical polishing that uses hazardous substances and is non-selective in processing area. Laser polishing addresses these challenges by using a high power laser spot to create a localised melt pool on the surface of the material. The surface tension drives the molten metal reducing the surface roughness once re-solidified. The small laser spot allows for selectivity in the processing area allowing multiple surface finishes. The dimensions of the components are defined from the build stage allowing for automation of the process increasing repeatability over other techniques.
The project has identified optimal parameters for laser polishing of titanium alloy and cobalt chrome and has progressed to polishing cranial and dental implants with a variety of sizes using a 100 W SPI fibre laser and a more cost effective fibre delivered laser diode array. We have also investigated methods of delivering beam onto internal surfaces using a prism. The tensile stresses produced in the polishing process have been relieved using standard heat treatment procedures.
Research Team: Mark W. McDonald, Wojciech S. Gora, Duncan P. Hand (HWU) Yingtao Tian (Lancaster), David Lunt (Manchester), Stuart G. Stevenson (Renishaw), Philip B. Prangnell (Manchester), Nick J. Weston (Renishaw)
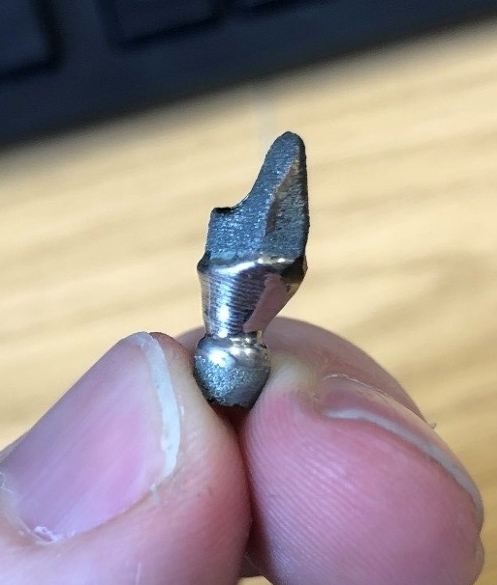
Point of contact: Prof. Duncan Hand
This project supported by Renishaw and EPSRC, is developing a laser polishing technique working to improve the surface finish of additively manufactured metal parts. This method offers advantages over currently used processing methods by allowing greater selectivity of the localised surface finish and simpler process automation for bespoke parts.
Additively manufactured components have a high surface roughness in their as-built state rendering them unsuitable for most applications without some degree of post-processing. Commonly used methods include mechanical polishing which for bespoke parts is a time-consuming semi-manual process requiring a skilled worker. Another common method is electro-chemical polishing that uses hazardous substances and is non-selective in processing area. Laser polishing addresses these challenges by using a high power laser spot to create a localised melt pool on the surface of the material. The surface tension drives the molten metal reducing the surface roughness once re-solidified. The small laser spot allows for selectivity in the processing area allowing multiple surface finishes. The dimensions of the components are defined from the build stage allowing for automation of the process increasing repeatability over other techniques.
The project has identified optimal parameters for laser polishing of titanium alloy and cobalt chrome and has progressed to polishing cranial and dental implants with a variety of sizes using a 100 W SPI fibre laser and a more cost effective fibre delivered laser diode array. We have also investigated methods of delivering beam onto internal surfaces using a prism. The tensile stresses produced in the polishing process have been relieved using standard heat treatment procedures.
Research Team: Mark W. McDonald, Wojciech S. Gora, Duncan P. Hand (HWU) Yingtao Tian (Lancaster), David Lunt (Manchester), Stuart G. Stevenson (Renishaw), Philip B. Prangnell (Manchester), Nick J. Weston (Renishaw)
Microscale Processes Governing Global Sustainability (MILEPOST)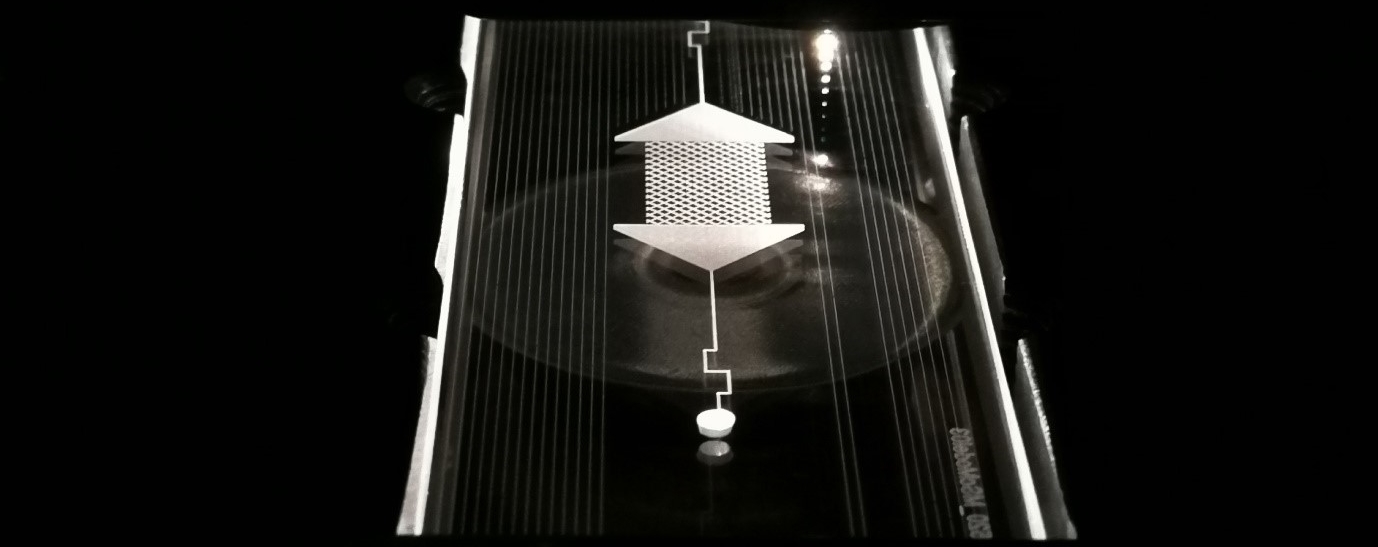
Point of contact: Prof. Duncan Hand
This ERC-funded project is focused on the investigation and understanding of fluid flow and transport processes in porous rocks, for carbon capture and storage applications. Our role in this project is to manufacture physical 3D models of porous rocks out of transparent materials, that can be used to verify theoretical models.
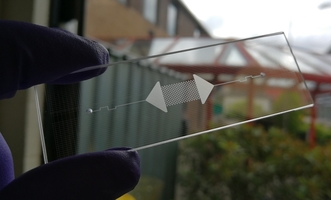
The MILEPOST project aims to investigate and fully understand the fluid flow and reactive transport mechanisms that govern the macroscopic behaviour of complex subsurface systems (porous rocks etc) at the pore level. Our part of this project is to use ultrafast lasers to manufacture transparent physical models of porous media, including up-scaled replicas of thin sections of realistic rock structures. A single picosecond laser is used to: (i) machine microstructures directly on a glass slide and (ii) enclose these microstructures by welding a second glass slide on top.
The ultimate goal of the MILEPOST project is the development of three-dimensional porous media models with integrated sensors for the in-vivo measurements of propagation fronts, such as pressure, pH change and fluid displacement. The outcome of this research will be used to better understand the subsurface fluid flow and reactive transport processes and to validate existing numerical models of subsurface systems.
The project is led by Professor Mercedes Maroto-Valer from the Research Centre for Carbon Solutions (RCCS) at Heriot-Watt University.
Research Team: Krystian Wlodarczyk, Amir Jahanbakhsh (RCCS), Omid Shahrokhi (RCCS), Rumbi Nhunduru (RCCS), Shima Ghanaatian (RCCS),
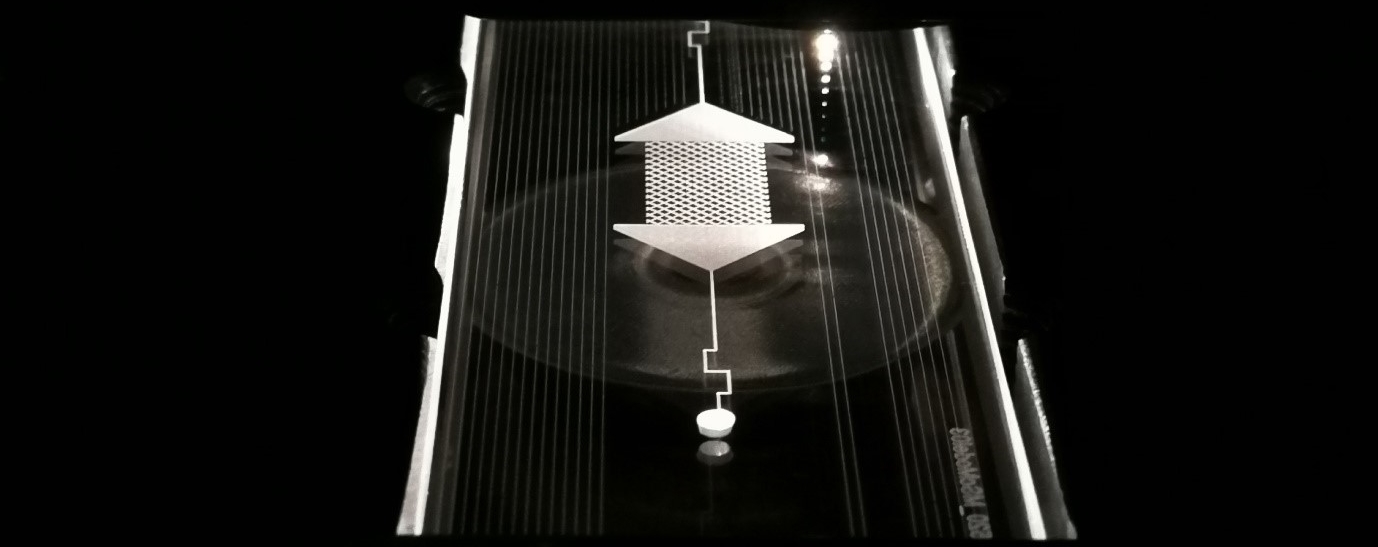
Point of contact: Prof. Duncan Hand
This ERC-funded project is focused on the investigation and understanding of fluid flow and transport processes in porous rocks, for carbon capture and storage applications. Our role in this project is to manufacture physical 3D models of porous rocks out of transparent materials, that can be used to verify theoretical models.
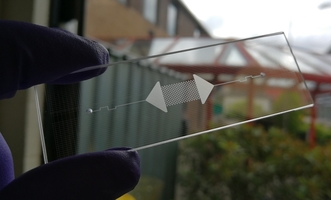
The MILEPOST project aims to investigate and fully understand the fluid flow and reactive transport mechanisms that govern the macroscopic behaviour of complex subsurface systems (porous rocks etc) at the pore level. Our part of this project is to use ultrafast lasers to manufacture transparent physical models of porous media, including up-scaled replicas of thin sections of realistic rock structures. A single picosecond laser is used to: (i) machine microstructures directly on a glass slide and (ii) enclose these microstructures by welding a second glass slide on top.
The ultimate goal of the MILEPOST project is the development of three-dimensional porous media models with integrated sensors for the in-vivo measurements of propagation fronts, such as pressure, pH change and fluid displacement. The outcome of this research will be used to better understand the subsurface fluid flow and reactive transport processes and to validate existing numerical models of subsurface systems.
The project is led by Professor Mercedes Maroto-Valer from the Research Centre for Carbon Solutions (RCCS) at Heriot-Watt University.
Research Team: Krystian Wlodarczyk, Amir Jahanbakhsh (RCCS), Omid Shahrokhi (RCCS), Rumbi Nhunduru (RCCS), Shima Ghanaatian (RCCS),
A Novel Approach to Manufacturing Lasers using Ultrafast Laser Welding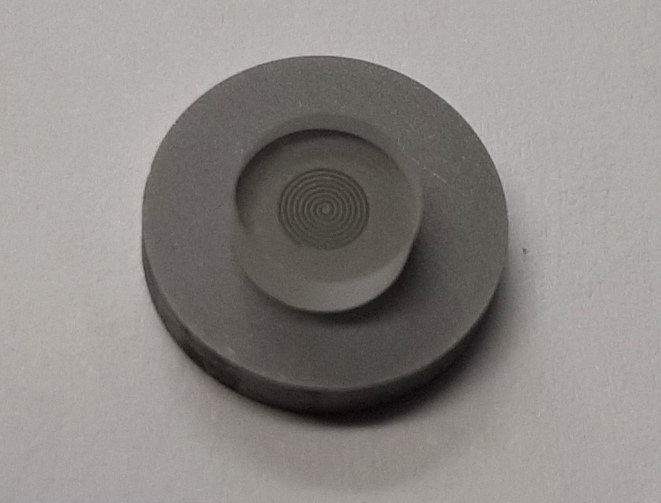
Point of contact: Prof. Duncan Hand
Heriot-Watt supported by Leonardo is investigating the use of Ultrashort pulse laser welding as a means of bonding laser crystals/optics to metallic support structures and heatsinks in order to fabricate a laser without the use of adhesives to bond dissimilar materials.
Adhesive bonding, used extensively within the fabrication of lasers and optical systems, has long been known to suffer from performance and reliability issues such as outgassing, accidental contamination of optical surfaces during bonding, creep and degradation with age. This project seeks to investigate the use of Ultrafast Laser Welding as an alternative to adhesives in the manufacture of lasers and other appropriate optical systems. The short pulse length of picosecond or femtosecond lasers allows for the bonding of highly dissimilar materials such as laser crystals/optics to metallic support structures and heatsinks. To assist with the evaluation of the validity of the bonds for use in optical systems, an automated circular polariscope has been developed as part of this project to measure the stress induced optical retardation of the welded components and its effect within the part.
Research Team: Samuel N. Hann, Duncan P. Hand, M. J. Daniel Esser, Robert Lamb (Leonardo), Ian Elder (Leonardo), Paulina O. Morawska, Richard M. Carter.
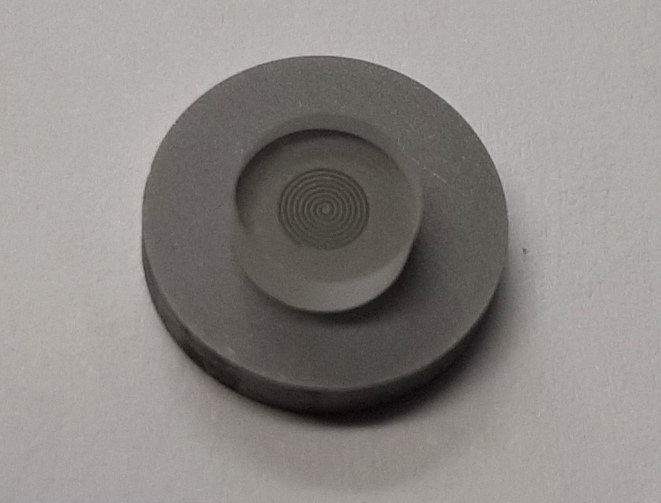
Point of contact: Prof. Duncan Hand
Heriot-Watt supported by Leonardo is investigating the use of Ultrashort pulse laser welding as a means of bonding laser crystals/optics to metallic support structures and heatsinks in order to fabricate a laser without the use of adhesives to bond dissimilar materials.
Adhesive bonding, used extensively within the fabrication of lasers and optical systems, has long been known to suffer from performance and reliability issues such as outgassing, accidental contamination of optical surfaces during bonding, creep and degradation with age. This project seeks to investigate the use of Ultrafast Laser Welding as an alternative to adhesives in the manufacture of lasers and other appropriate optical systems. The short pulse length of picosecond or femtosecond lasers allows for the bonding of highly dissimilar materials such as laser crystals/optics to metallic support structures and heatsinks. To assist with the evaluation of the validity of the bonds for use in optical systems, an automated circular polariscope has been developed as part of this project to measure the stress induced optical retardation of the welded components and its effect within the part.
Research Team: Samuel N. Hann, Duncan P. Hand, M. J. Daniel Esser, Robert Lamb (Leonardo), Ian Elder (Leonardo), Paulina O. Morawska, Richard M. Carter.
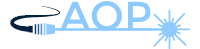