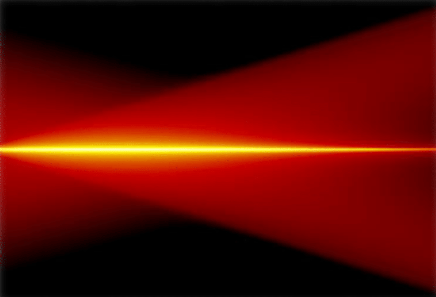
The True Potential of Laser Based Manufacturing
Point of contact: Dr Richard Carter
Manufacturing with lasers has advanced from the purely science fiction ideas of the 1950’s and 60’s to be a real world, critical step, in the manufacture of an enormous range of products. Over the years a range of new techniques and processes have been developed in research labs and companies across the world. One of the more important of these has been the development of beam-shaping technology.
Laser processing of material is driven by transfer of energy from the laser beam into the material, and can be a mixture of thermal, photo-chemical and optical non-linear effects. By changing the shape of a laser beam where it impacts a material it is possible to mould how and where energy is transferred. This then allows for more precise control of the laser-material interaction and hence of the manufacturing process itself.
This has led to improvements in the way cutting, welding and similar processes work with improvements in quality and efficiency. However these beam-shaping technologies are limited. They only shape in two dimensions, i.e. in a single focal plane. This is not a big problem for “surface processes” as the plane at which the laser beam is formed into the right shape can be made, with some care in focussing the beam, to be the surface of the material. However for materials with an irregular shape, imprecise thicknesses, or that are at least partially transparent to the laser, this is a challenge. It is also a challenge when trying to take advantage of the range of exciting new technologies based on non-linear phenomena.
Non-linear laser processes typically limit the laser material interaction to only those regions of the laser beam where there is an extremely high intensity i.e. at the focus. By moving the focus inside the material it then possible to manufacture from the inside out. However, because the light interacts with the material not just on the surface but throughout the focal volume two dimensional beam shaping is insufficient; full 3D control is instead required.
Within this research project we will take advantage of the wave-nature of light. Through careful shaping of a glass optic it is possible to bend different parts of a laser beam to overlap in a controlled manner. As the beams overlap they will interfere creating regions of high and low energy. Though careful calculation it is possible to manipulate this with each optic designed to give a precise interference pattern which results in a specific energy distribution; to shape the beam in three dimensions.
By shaping the laser beam throughout the focal region it will be possible to open entirely new methods of manufacture from more effective means to cut toughened glass (like mobile phones or iPads), dice and drill semiconductors (for computer chips), make precision medical devices, and create new and much more effective surgical procedures. The potential applications are truly enormous, transformative and will change how and what we can manufacture.
This is a 3 year EPSRC funded project with researchers affiliated with the AOP group, (EP/V006312/1 £586k).
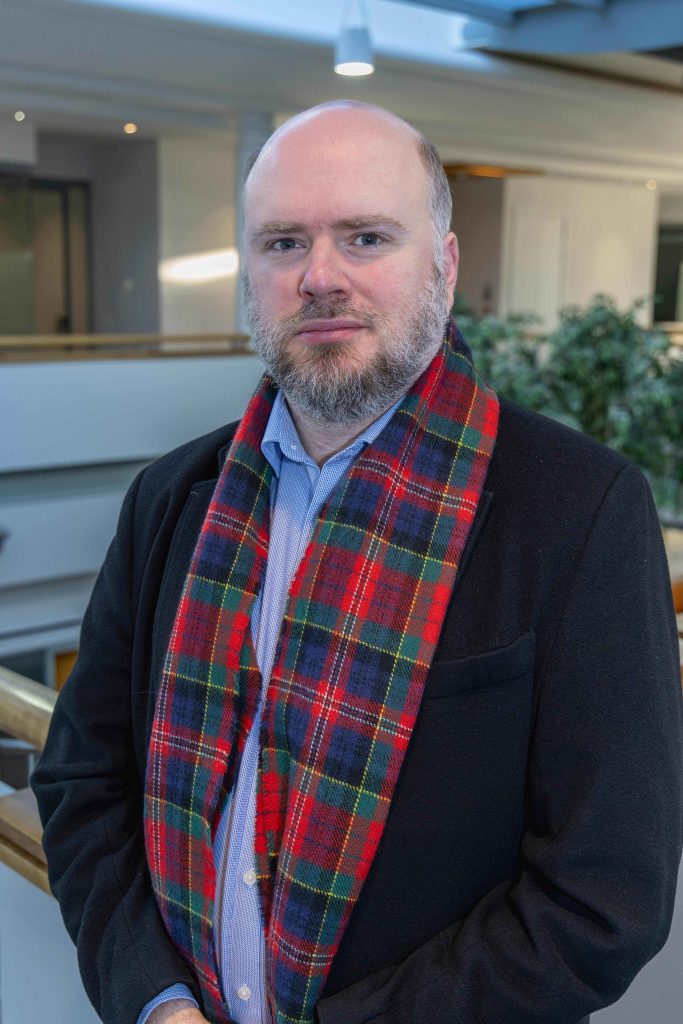
Richard Carter
Project Lead
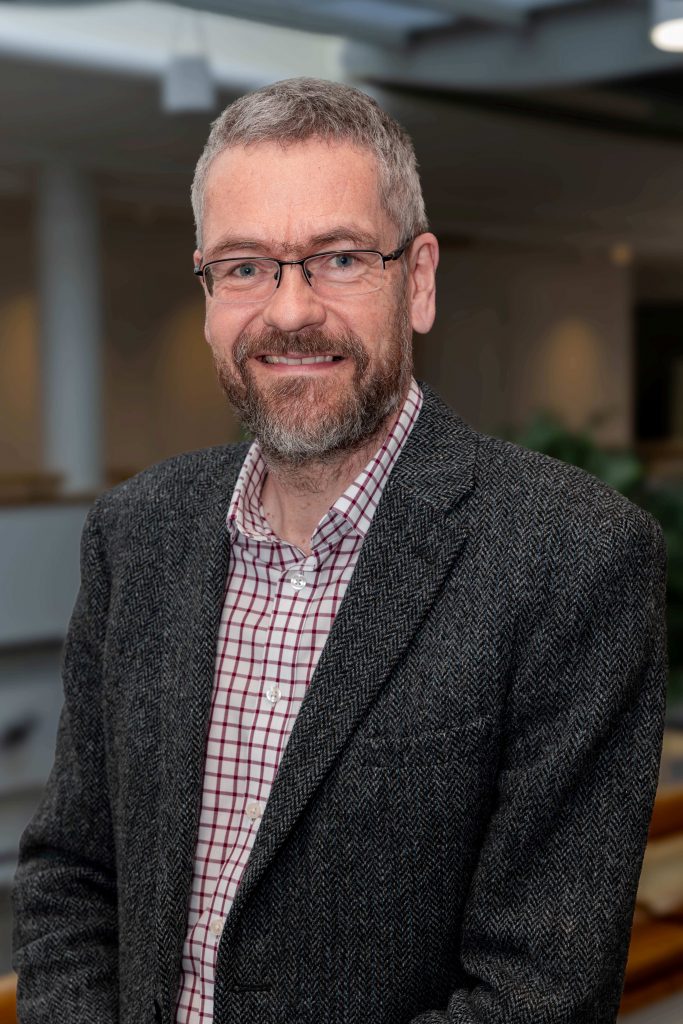
Duncan Hand
Co-Investigator
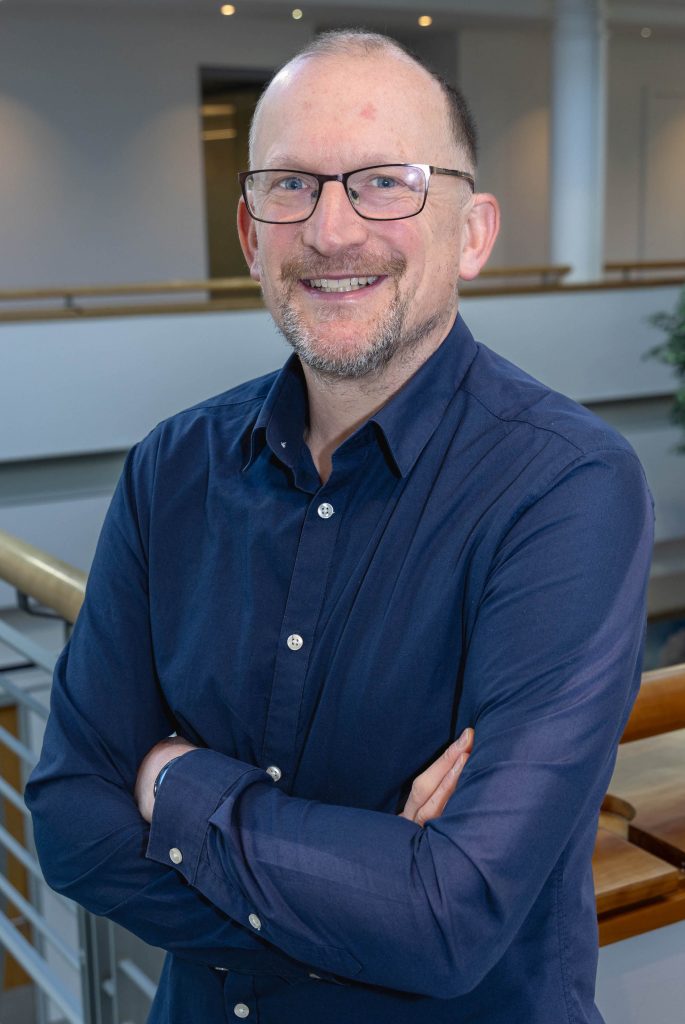
Jon Shephard
Co-Investigator
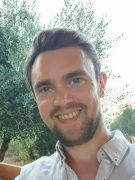
Calum Brown
PDRA
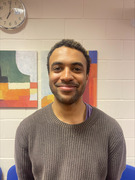
Jakob Gueye
PhD
Collaborators: M. J. Daniel Esser (HWU), Leonardo MW, Luxinar, GTS, NSG Group (UK), Oxford Lasers, The Manufacturing Technology Centre (MTC)
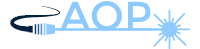